IJCRR - 4(14), July, 2012
Pages: 90-95
Date of Publication: 31-Jul-2012
Print Article
Download XML Download PDF
ETHANOL AS ALTERNATIVE FUEL FOR SI ENGINE - A REVIEW
Author: Abhishek Prakash Verma, Alok Choube
Category: Technology
Abstract:The main objective of this review paper is to find effect of Ethanol (ethyl alcohol) as alternative fuel in SI engines. Since Ethanol possesses characteristic, properties that have positive influence on engine performance as well as exhaust emissions. This paper shows how ethanol can be used as fuel for SI Engines, Study is based on technical as well as quantitative data available from different researches. This Review paper is focused on two broad groups namely, effect of compression ratio and effect of ethanol blends on engine performance.
Keywords: Ethanol, Variable compression ratio, blending Fuel, Alternative fuel
Full Text:
INTRODUCTION
As we know the oil crisis led many countries to search for alternative fuels to substitute conventional fuels which is clean, renewable and sustainable. Ethanol is one of the good alternative to it, since it possesses antiknock characteristics, which allow higher compression ratio, and consequently higher engine output power, also characteristics that are relevant to its environmental performance in combustion as a motor fuel[13]. The exhaust gas from SI Engine contain not only normal product of nitrogen, water vapour, and carbon dioxide but also contain carbon monoxide, hydrogen oxygen, unburned gasoline, and other traces of hydrocarbons plus traces of aldehydes, alcohols ketones , etc [20]. Although fossil fuel have became the dominating energy resource for the modern world. alcohol has been used as a fuel through history, the first four aliphatic alcohol (methanol, ethanol propanol, butanol) are the area of interest as they can be synthesized biologically[2] and they have characteristics which allow them to use in now a day's automotive engines. Ethanol is a known ?octane enhancer‘ and ?oxygenate‘. An octane enhancer is a component added to petrol to increase the research octane number (RON) and to reduce engine knock. An oxygenate is a fuel octane component containing hydrogen, carbon and oxygen in its molecular structure.
Bio- Fuel Ethanol
There is no chemical difference between biologically produce alcohol and those obtain from other resources. Due to the high evaporation heat, high octane number and high flammability temperature, ethyl alcohol has positive influence on the engine performance and increases the compression ratio. Variable compression [ 19] Ethanol can be used as an automotive fuel by itself and can be mixed with petrol to form an ethanol/petrol blend. The most common uses are: a) 10% ethanol (known as E10); b) 85% ethanol (known as E85); This blend is used in some states of the US and requires particular vehicle technology known as ?Flexible Fuel Technology‘ (FFT). c) 20 - 24% ethanol (known as E22); d) 100% ethanol (E100); This is also used in Brazil and requires vehicle technology dedicated to the fuel.
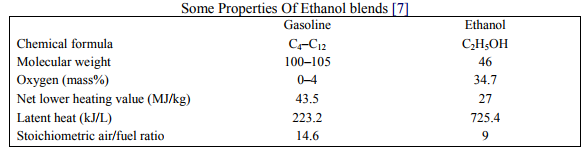
Literature Review
Effect of Compression ratio on engine performance : Rodrigo93 [4] presents the effect of compression ratio on engine performance, parameter evaluated were brake mean effective pressure power, specific fuel consumption thermal efficiency exhaust gas temperature volumetric efficiency. In this the effect of compression ratio on the performance of an engine fuelled by hydrous ethanol have been investigate. The result shows that high compression ratio increases cylinder pressure thus increasing the work done on the piston and consequently torque and brake mean effective pressure . Ethanol was used as fuel at high compression ratio to improve performance and to reduce emissions in a small gasoline engine with low efficiency Experiments in variable compression ratio singlecylinder engines fuelled by blends of gasoline and ethanol with different concentrations have been performed by Celik [13], In his study, initially, the engine whose compression ratio was 6/1 was tested with gasoline, E25 (75% gasoline + 25% ethanol), E50, E75 and E100 fuels at a constant load and speed. It was determined from the experimental results that the most suitable fuel in terms of performance and emissions was E50. Then, the compression ratio was raised from 6/1 to 10/1. The engine was tested with E0 fuel at a compression ratio of 6/1 and with E50 fuel at a compression ratio of 10/1 at full load and various speeds without any knock. The experimental results showed that engine power increased by about 29% when running with E50 fuel compared to the running with E0 fuel. Moreover, the specific fuel consumption, and CO, CO2, HC and NOx emissions were reduced by about 3%, 53%, 10%, 12% and 19%, respectively. Yuksel [5]. attempted to determine a suitable ethanol-gasoline blend for spark ignition engine operation, varying compression ratio. Engine output power and HC emissions were optimized with compression ratio 6:1 and 2000 rev/min, using E50 as fuel. With increasing ethanol concentration in the fuel, specific fuel consumption continuously increased, while CO, CO2 and oxides of nitrogen (NOx) emission levels were decreased. The result shows operating the engine with E50 and compression ratio 10:1 simultaneously improved all engine performance and emission parameters in comparison with gasoline and compression ratio 6:1. In the experimental study of Al-Hasan [12], the effects of usage of unleaded gasoline–ethanol blends on spark ignition engine performance and exhaust emission were investigated. The results showed that ethanol addition leads to an increase in brake power, brake thermal efficiency, volumetric efficiency and fuel consumption by about 8.3%, 9%, 7% and 5.7% mean average values, respectively. The best result at the engine performance and exhaust emissions was obtained by usage of 20% ethanol fuel blend. Topgul[7]the effect of compression ratio on engine performance and exhaust emissions was examined at stoichiometric air/fuel ratio, full load and minimum advanced timing for the best torque MBT in a single cylinder, four stroke, with variable compression ratio and spark ignition engine The fuels containing high ratios of ethanol; E40 and E60 had important effects on the reduction exhaust emissions. The maximum decrease was obtained with E40 and E60 fuels at 2000 rpm engine speed. Mustafa [14] shows the effects of unleaded gasoline (E0) and unleaded gasoline–ethanol blends (E50 and E85) on engine performance and pollutant emissions were investigated experimentally in a single cylinder four-stroke spark-ignition engine at two compression ratios (10:1 and 11:1). The engine speed was changed from 1500 to 5000 rpm at wide open throttle (WOT). The results of the engine test showed that ethanol addition to unleaded gasoline increase the engine torque, power and fuel consumption and reduce carbon monoxide (CO), nitrogen oxides (NOx) and hydrocarbon (HC) emissions. Bakhatyar [6 ] It was also found that ethanol–gasoline blends allow increasing compression ratio (CR) without knock occurrence. Owen and Coley [11] pointed out as one of the main advantages over hydrocarbon fuels, allowing for the use of higher compression ratios and, consequently, the production of higher engine output power. Osman et.al. [1] investigated the effect of ethanol–gasoline blends (E10, E20, E30 and E40) on engine performance and emissions at various compression ratios (8, 10, and 12). For each fuel blend, there is an optimum compression ratio that gives maximum indicated power. In this study, optimum compression ratios were found to be 8, 10 and 12 for E10, E20 and E30 fuels, respectively. Celik [13] carried out study to determine the suitable ethanol–gasoline blend rate in terms of performance and emissions for small engines, and to investigate experimentally the improvement of the performance and emissions by testing the engine with suitable ethanol–gasoline blend fuel at high compression ratio without any knock. Ibraham[9 ] The experiments in engine fuelled with four types of fuels blends included the brake power, brake thermal efficiency, exhaust temperature, and brake fuel consumption under various speeds, test runs were made on straight gasoline fuel in order to make comparative assessments The brake power of the engine increases with the engine speed increases for all fuels
Effect of Ethanol on Engine Performance
Zlata [18] pointed out the characterized evaluation of hydrocarbon composition, vapour pressure increases due to formation of azeotropes. The water solubility was increased with higher unsaturated hydrocarbons in petrol also the ethanol content in petrol blend was decreased by water extraction. Ceviz and Yuksel [15] shows that A small amount of cyclic variability (slow burns) can produce undesirable engine vibrations. On the other hand, a larger amount of cyclic variability (incomplete burns) leads to an increase in hydrocarbon consumption and emissions. This paper investigates the effects of using ethanol–unleaded gasoline blends on cyclic variability and emissions in a spark-ignited engine. Results of this study showed that using ethanol–unleaded gasoline blends as a fuel decreased the coefficient of variation in indicated mean effective pressure, and CO and HC emission concentrations, while increased CO2 concentration up to 10vol.% ethanol in fuel blend. On the other hand, after this level of blend a reverse effect was observed on the parameters aforementioned. The 10vol.% ethanol in fuel blend gave the best results. Costa and Sodré [4] compared hydrous ethanol and gasoline ethanol blend (E22) with regard to engine performance and exhaust emissions. The use of hydrous ethanol slightly improved engine torque and output power at high engine speeds, but, due to its lower heating value, it also increased specific fuel consumption in comparison with gasoline. Thermal efficiency was higher when ethanol was used instead of gasoline, as combustion duration was shorter. CO and HC emissions were reduced when ethanol was used, once the presence of oxygen in the ethanol molecule helps to oxidize those components; however, NOx emissions were increased, as higher combustion temperatures were attained. The engine performance and the pollutant emission of a commercial SI engine were investigated by using an ethanol–gasoline blend fuel [5]. Experimental results indicated that using ethanol–gasoline blended fuel, the torque output consumption an increase in the specific fuel consumption and a decrease in the engine torque and power output measurements were observed. Mostly alcohol react with rubber, copper, brass parts which cause a jam in the fuel pipe. Therefore, it is advised to use fluorocarbon rubber as a replacement for rubber[17,21] Owen and Coley[11].The anti-knock characteristic of alcohols was pointed out, also the higher heat of vaporization of alcohols under high temperatures and the faster flame speed permit increased fuel conversion efficiency in comparison with gasoline. Moreover, alcohol combustion generates higher product volume, thus increasing cylinder pressure and the work done on the piston. On the other hand, the smaller low heating value of alcohols results in increased specific fuel consumption in comparison with gasoline, i.e. a higher mass amount of alcohol is required per unit power produced. Cold start is also a problem for alcohol fuels, due to their low vapour pressure Hesis et al. [16] tested fuel with 99.9 pure Ethanol in volumetric ratios 0-30% with gasoline, nearly same torque was obtain with different ratios of ethanol gasoline blends when compared with gasoline E0, better combustion can be achieved and higher torque can be obtain. Topgul et al. [5] examined the effects of ethanol– gasoline blends (E0, E10, E20, E40, E60) and ignition timing on performance and emissions. The result showed that the brake torque slightly increased, and CO and HC emissions decreased with ethanol–gasoline blend was. It was also found that blends with ethanol allowed the compression ratio to increase without any knock. Rong [20] shows the effects of ethanol gasoline blended fuel on cold-start emissions of an SI engine, the engine could be started stably with E5, E10, E20, and E30. The HC and CO emissions decreased significantly with more ethanol than 20% added. However, for E40 the engine idling became unstable because the air-fuel mixture was too lean. C. Ananda[3] examined effects of ethanolblended gasoline with oxygenated additives on a multi – cylinder Spark Ignition (SI) Engine. The experiments were conducted in two stages. The experimental results proved that the blend increased brake thermal efficiency more than a sole fuel, such as gasoline. The emission tests found that the CO slightly decreased, while HC and O2 increased moderately and CO2 and NOx appreciably decreased. Exhaust gas recycle (EGR) is the principal technique used for control of SI engine NO, emissions A fraction of the exhaust gases are recycled through a control valve from the exhaust to the engine intake system. The recycled exhaust gas is usually mixed with the fresh fuel-air mixture just below the throttle valve. EGR acts, at part load, as an additional diluents in the unburned gas mixture, thereby reducing the peak burned gas temperatures and NO formation rates.[10]
CONCLUSION
From the literature review, it is understood that there are slight increases or decreases in Engine performance when the ethanol and ethanol– gasoline blends are used at the original compression ratio in the engines, Emissions like CO, HC, and NOx decrease.. At higher compression ratio, power increases and fuel consumption decreases, and increase in thermal efficiency when hydrous ethanol was used [4]. The compression ratio of air-cooled small engines is low, in air-cooled small engines, exhaust gas temperature are higher [5] the knock tendency is also higher. Thus, the compression ratio is kept lower in these engines to prevent knock. Ethanol addition to gasoline leads to leaner operation and improves combustion ,Engine performance parameters such as effective power and effective efficiency increase with increasing ethanol amount in the blended fuel as a result of improved combustion[6]. Significant improvements can be obtained in power and efficiency if the small engines with low compression ratio can be run at higher compression ratios using fuels resistant to the knock. Ethanol has high octane number, both permits the rising of the compression ratio and gives lower emission. The bio- ethanol is a suitable substitute for fossil fuel whose reserve is limited , since Ethanol is also eco friendly fuel, easily available, cheaper than gasoline.
ACKNOWLEDGEMENT
Author acknowledge the immense help from the scholar whose article are cited and included in reference of this manuscript. The author are also grateful to author/editors/ publisher of all those article, journal, and books from where the literature for this article has been reviewed and discussed.
References:
1. A.A. Abdel-Rahman, M.M. Osman, Experimental investigation on varying the compression ratio of SI engine working under different ethanol–gasoline fuel blends, International Journal of Energy Research 21 (1997) 31–40
2. Carlos A. Cardona, Oscar J. Sanchez, Fuel ethanol production: Process design trends and integration opportunities
3. C. Ananda Srinivasan and C.G. Saravanan Study of Combustion Characteristics of an SI Engine Fuelled with Ethanol and Oxygenated Fuel Additives Journal of Sustainable Energy & Environment 1 (2010) 85-91
4. Costa RC, José R. Sodré, Compression ratio effects on an ethanol/gasoline fuelled engine performance, Applied Thermal Engineering 31 (2011) 278-283
5. Fikret Yu ksel , Bedri Yuksel, The use of ethanol–gasoline blend as a fuel in an SI engine, Renewable Energy 29 (2004) 1181– 1191
6. Hakan Bayraktar, Experimental and theoretical investigation of using gasoline– ethanol blends in spark-ignition engines Renewable Energy 30 (2005).
7. Hu seyin Serdar Yu cesu , Tolga Topgul, Can Cinar, Melih Okur, Effect of ethanol–gasoline blends on engine performance and exhaust emissions in different compression ratios, Applied Thermal Engineering 26 (2006) 2272–2278
8. H. Serdar Yucesu , Adnan Sozen , Tolga Topgul , Erol Arcaklioglu, Comparative study of mathematical and experimental analysis of spark ignition engine performance used ethanol–gasoline blend fuel
9. Ibrahim Thamer Nazzal Experimental Study of Gasoline –Alcohol Blends on Performance of Internal Combustion Engine European Journal of Scientific Research ISSN 1450- 216X Vol.52 No.1 (2011), pp.16-22
10. J.B. Heywood, Internal Combustion Engine Fundamentals. McGraw-Hill Book Company, Singapore, 1988
11. K. Owen, T. Coley, Automotive Fuels Reference Book, second ed. Society of Automotive Engineers, USA, 1995.
12. M. Al-Hasan, Effect of ethanol–unleaded gasoline blends on engine performance and exhaust emission, Energy Conversion and Management 44 (9) (2003) 1547–1561
13. M. Bahattin Celik, Experimental determination of suitable ethanol–gasoline blend rate at high compression ratio for gasoline engine, applied thermal eng. 28(2008) 396-404.
14. Mustafa Koç a, Yakup Sekmen b, Tolga Topgul c, Hu seyin Serdar Yucesu , The effects of ethanol–unleaded gasoline blends on engine performance and exhaust emissions in a spark-ignition engine, Renewable Energy 34 (2009) 2101–2106
15. M.A. Ceviz, F. Yüksel, Effects of ethanolunleaded gasoline blends on cyclic variability and emissions in a SI engine, Appl. Therm. Eng. 25 (2005) 917e925.
16. W. Hsieh, R. Chen, T. Wu, T. Lin, Engine performance and pollutant emission of an SI engine using ethanol–gasoline blended fuels, Atmospheric Environment 36 (3) (2002) 403– 410
17. Naegeli DW, Lacey PI, Alger MJ, Endicott DL. Surface corrosion in ethanol fuel pumps. SAE paper 971648
18. Zlata Muzikova , Milan Pospisil, Gustav Sebor, Volatility and phase stability of petrol blends with ethanol, Fuel 88 (2009) 1351– 1356
19. Environment Australia 2002, Setting the Ethanol Limit in Petrol, ISBN: 0 642 54804 8
20. Rong-Horng Chen, Li-Bin Chiang , ChungNan Chen , Ta-Hui Lin Cold-start emissions of an SI engine using ethanol gasoline blended fuel
21. V Ganesha internal combustion engine Tata Mc-graw hills 22. Edward F Obert, Internal combustion engines and air pollution , Harper International Edition
|