IJCRR - 3(7), July, 2011
Pages: 84-88
Print Article
Download XML Download PDF
SEA WATER ABSORPTION PHENOMENON IN BANANA FIBRE REINFORCED VINYL ESTER COMPOSITES
Author: Rajesh Ghosh, A Ramakrishna, G.Reena
Category: Technology
Abstract:The ageing response of banana fibre reinforced vinyl ester composites in sea water environment is investigated. The main objective was to evaluate the effects of sea water on the mechanical properties. Fibre mats were reinforced into vinyl ester matrix and composite laminates were made. These were then subjected to sea water ageing and water absorption and mechanical properties were tested. It is observed that during the initial stages there was increased rate of water absorption following the Fickian law. On prolonged time of immersion, moisture absorption led to plasticization of the matrix and also reduced the mechanical properties of the specimen.
Keywords: Sea water, absorption, banana fibre, vinyl ester.
Full Text:
INTRODUCTION
Fibre reinforced polymers are increasingly shown interest from the engineering and structural view point. A lot of work is done and investigated on glass fibre reinforced composites. But glass fibre has a detrimental effect on the environment and hence there is a growing interest on bio fibres on the possibility of replacing glass fibres. These composites are being used for marine applications such as water storage vessels, pipelines, small boats etc. Researchers found that prolonged exposure of glass fibre composites caused degradation in flexural strength and modulus [1, 2]. It is observed that the polymer matrix gets degraded by a hydrolysis reaction of the unsaturated groups within the resin [3]. Vinyl ester composites show superior chemical stability in sea water atmosphere [4, 5]. The absorption of water into the macromolecular network of a thermoset matrix causes swelling and plasticization of the matrix [6- 8]. Researchers have reported that absorption of water (distilled or sea water) causes changes in the thermophysical and mechanical properties by plasticization and hydrolysis [9, 10]. It is reported that degree of degradation depends on the degree of crosslinking of the polymers [11]. Moisture may also affect the fibers. Experimental work is done on glass fibre reinforced in epoxy or vinyl ester resin. But much work is not done on banana fiber reinforced in polymer matrix and the composite exposed to sea water environment. In the present work banana fibre reinforced vinyl ester composite specimens were immersed in sea water and the moisture gain is noted and compared with distilled water moisture gain.
EXPERIMENTAL
Banana fibers were procured from Tamil Nadu - India. The fibers were knitted in the form of mats. The mats were alkali treated. Vinyl ester is procured from ECMAS India pvt ltd. Composites were made by hand layup process in an MS die with inner cavity of dimensions 200mm x 200mm x 10mm. These laminates were later oven cured. Composite specimens were later cut to size as per ASTM standards. The cut edges of the specimens were coated with a thin layer of adhesive.
Sea water absorption tests: These specimens were first weighed and then immersed in sea water taken from the coast of Visakhapatnam – India (Bay of Bengal). Specimens were periodically taken out of the water; the surface is wiped with a tissue paper and weighed in an electronic balance. The water uptake was plotted against square root of immersion time.
The moisture absorbed M (in %) is calculated using
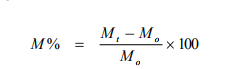
The moisture absorbed M (in %) is calculated using where Wt is the measured weight of the specimen at time t and Wo is the initial dry weight of the specimen.
RESULTS AND DISCUSSION
The water absorption into the composite specimen may be considered to be following three different modes. The principal mode being the diffusion of water molecules into the microgaps of the resin, while the other processes being capillary action through the interfacial gap between the fibre and the resin and also through the fiber, and transport of water through the microcracks in the matrix. The diffusion, in most of the cases, follows the equation
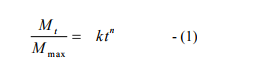
where Mt is the moisture content at time t, Mmax is the maximum moisture content at saturation and k and n are constants. The diffusion coefficient is an important parameter in Fick‘law. This can be found out from the following equation
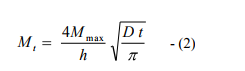
where Mt , Mmax and t are as denoted above, and h is the specimen thickness. The diffusion coefficient can be found out by considering the slope of the first portion of the curve between moisture gain and square root of time by the following equation.

where k is the initial slope of the plot. Fig.1 represents the percentage moisture gain plotted against square root of time. The analysis of diffusion mechanism and kinetics can be performed by modifying eqn.(1) as shown below

Fig.2 shows the graph plotted against log(Mt / Mmax) against log(t).
The straight line in Fig.2 shows the fitting of the experimental data to eqn. (3). The values of k and n resulting from the graph in fig.3 is found to be 0.001254 and 0.59 respectively. The value of ?n‘ suggests that the initial diffusion follows Fick‘s law. The diffusion coefficient was found to be 2.67 x 10-6 mm2 /sec.
Effect of sea water on mechanical properties:
Tensile properties: Tensile test is done according to ASTM D638. The tests were carried out in a Hounsfield tensometer model H20KW. The cross head speed is 1mm/min.
Flexural properties: The flexural test is done according to ASTM D790 in a universal testing machine by UNITED calibration corp. with a cross head speed of 0.5mm/min. Fig.4 shows the values of tensile strength, tensile modulus, flexural strength and flexural modulus of the composite specimens before and after immersion in sea water. Sea water diffuses into the composite specimen following the Fick‘s law of diffusion initially. With elapsing time, the salts get deposited into the microcracks preventing further seepage. Hence the rate of water absorption slows down with time. With the ingress of water, the mechanical properties decrease as understood from the graphs.
CONCLUSION
The water uptake increases rapidly during the initial stages. The absorption process follows the Fickian diffusion process during the initial stages but later it follows non-fickian diffusion process due to the deposition of the salts present in the water. Absorption of sea water causes the deterioration of mechanical properties. The tensile strength is found to decrease by 6.46 % and the flexural strength is found to decrease by 12.19 %. There is a decrease in the tensile modulus and flexural modulus of the specimen by 12.32% and 10.09%.
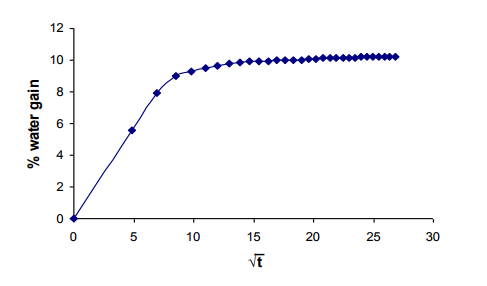
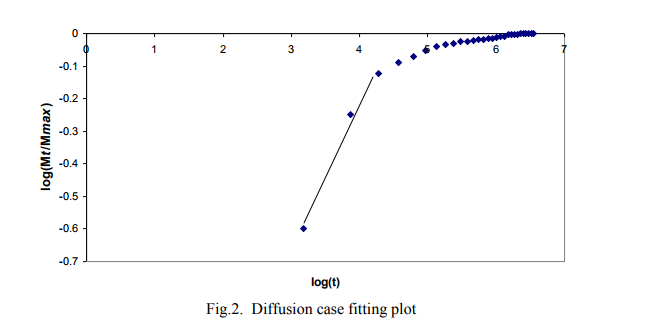
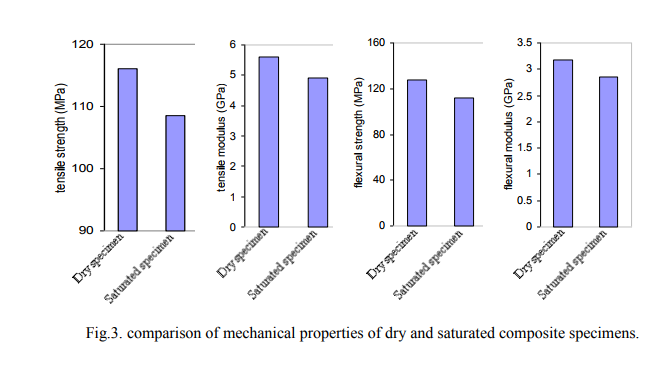
References:
1. Kootsokoos A, Mouritz AP, ?Sea water durability of glass and carbon polymer composites. Compos. Sci. Technol. 64, 1503-1511 (2004)
2. Gellert EP, Turley DM, ?Seawater immersion ageing of glass fibre reinforced polymer laminates for marine applications.? Composites 30A, 1259 (1999)
3. Srinivas MV, Dvorak GJ and Prochazka P, ?Design and fabrication of submerged cylindrical laminates – II, Effects of fibre pre-stress. International journal of solids and structures. 36, 3945 – 3976 (1999).
4. Apicella A, Migliaresi C, Nicholais L and Roccotelli S, ?The water ageing of unsaturated polyester based composites: Influence of resin chemical structure, Composites. 14, 4, 387 – 392 (1983).
5. Dvorak GJ, Prochazka P, and Srinivas MV, ?Design and fabrication of submerged cylindrical laminates – I, International journal of solids and structures. 36, 3917 – 3943 (1999).
6. Bradley WL, (1995). J. Mater. Sci 30:5537. doi:10.1007/BF00351570.
7. Pomies F, Carlsson LA, Gillespie JW Jr (1995) ASTM STP 1230. philadelphia.
8. Springer GS (ed) (1981) Environmental effects on composite materials, Technomic, CA.
9. Ellyin F, Rohrbacher C, ?Effect of aqueous environment and temperature on glass fibre epoxy resin composites?. J. Reinf. Plast. Compos. 19(17), (2000)
10. Wood C, Bradley WL, ?Determination of the effect of sea water on the interfacial strength of an interlayer eglass/graphite/epoxy composite by in situ observation of transverse cracking in an environmental SEM. Compos. Sci. Technol. 57, 1033 – 1043, (1997)
11. Rutowska M, Krasowska K, Heimwoska A, Steinka E, Janik H, ?Degradation of polyurethanes in sea water?. Polym. Degrad. Stab. 76, 233 – 239 (2002)
|