IJCRR - 4(6), March, 2012
Pages: 166-173
Print Article
Download XML Download PDF
MEANS OF LIVELIHOOD AMONG THE WEAVER COMMUNITY OF SHANTIPUR OF NADIA DISTRICT
Author: Pradipta Dubey, Subhrangsu Santra
Category: General Sciences
Abstract:The history of handloom of Santipur of Nadia district has long dating back from 15th Century; Where Santipur was placed as the centre of Vaishnavite culture and Bhakti movement. Even at present handloom is the closest contestant of the primary sector i.e. agriculture. People earn their more or less same income through preparing shrees than agriculture activities, even some time more from earlier then latter. Though the main share of profit goes to the middlemen, still they are acting as bread provider. The installation charge of a loom is so high which is not possible for any individual in backward class communities to own it and perform their own business. Even if possible the same, but not possible to get raw materials and to market the final product by the poor people. The present paper seeks to find out the Cost and Benefit of individual weaver as well as middlemen in the locality involved in the activity. Finding shows that land less poor families got an opportunity to maintain their livelihood through handloom. Middlemen also received the maximum portion of the profit. Still it is not possible to remove the middlemen without finding an alternative who can take the responsibility to supply raw materials and marketing the final product. Again study suggested that it can only be possible through Public-Private partnership.
Keywords: Shantipur, Handloom, Middlemen, Livelihood, Cost and benefit
Full Text:
INTRODUCTION
The dispersed, unorganized and often household based micro and small enterprises are capital-saving, labourintensive, and eco-friendly avenues of livelihood. In India, they are the largest sources of employment after agriculture and are found in both rural as well as urban areas. In nearly three decades, the structure of rural employment has not changed much.1 Symbolically for Indian culture and heritage, handlooms cater to 65 lakh persons for their living by skilfully blending myths, faiths, symbols, and imagery. Today, the handloom industry directly and indirectly provides livelihood to 124 lakh people, of which 60% are women while 12% belongs to Scheduled Caste category and 20% from Scheduled Tribe (Ministry of Textiles, 2001). Majority of them have no cultivable land or other assets. While the exact numbers are not available, a major portion of the handloom weavers belong to minority communities. Indian handloom products range from coarse cloth to very fine fabrics from a variety of fibres such as cotton, silk, tasar, jute, wool, and synthetic blends. Each region has its signature handcrafted textiles that are unique in design and style. What is woven is, however, inseparable from where and how it was woven, that was from the structure of production. There were independent weavers, weavers organized into co-operatives, and there were those working under master weavers. Present Situation With the largest number of handlooms in the world, India produces approximately 6541 million sq m of handloom cloth annually. While the total production of cloth has increased by about 30% between 1996–97 and 2004–05, the production of handloom sector has declined by about 23%. Between 2000 and 2005, the average annual growth rate of handloom production has been 6.99%. West Bengal, Tamil Nadu, Uttar Pradesh, Andhra Pradesh, Assam, and Manipur are the major handloom States and accounting 75% of handloom weaving in the country. As per the Second Handloom Census, (1995-96) Assam (10.97 lakh), West Bengal (2.22 lakh), and Manipur (2.15 lakh) together accounted for 64% of the handloom units. Almost all handloom production in India is for domestic markets. According to the Directorate General of Handlooms, though handlooms account for 10% of our textile exports, only 1.3% of working looms produce fabric for export markets. Europe is the largest destination, accounting for nearly half of the total exports in 1999–2000.
The bustling town of Shantipur in Nadia district of West Bengal, India, is just 90 kilometres (2 hours drive away from Kolkata, the capital city of West Bengal) north of the metropolis of Kolkata. It has recently gained the status of municipality. Neighbouring Fulia, still a village is often uttered in same breath with Shantipur, their contrasting backgrounds notwithstanding. Together they are perhaps the most renowned Bengal handloom saree weaving centre in Bengal. Shantipur and Fulia sarees are household names across India. Shantipur – Fulia region has over 125,000 handlooms, churning out Shantipuri, Tangail, and Jamdani handloom sarees in a variety of yarns like cotton, tussar and silk. Dhotis, dress materials, stoles and scarves are also woven. History There are records of handloom saree weaving activity in Shantipur, a centre of Vaishnavite culture and Bhakti movement2 , as early as the 15th century. Weaving flourished throughout the medieval era, and the famed indigo-dyed Neelambari (of a particular saree, name derived from Neel, its blue colour) made the Shantipur saree a household name. There is a strong sense of identity among Shantipur weavers. They united to agitate against the stranglehold of the Dadni system of the British East India Company and even took their grievances to colonial courts during the19th century3 . In the decades leading up to independence several innovations were introduced in the loom and pattern of weaving, Shantipur saw gradual inflow of techniques like the Barrel Dobby, facilitating the conversion from Throw Shuttle to Fly Shuttle (1920s), the Jacquard Machine (1930s), and sectional warping and sizing that allowed production of warp yarns 350 yards long (1930s).4 Traditional Styles Shantipur saree: The ?Neelambari‘ saree was the first product that made Shantipur famous. The indigo dyed, midnight blue cotton handloom saree was so alluring that it was called ?an enemy of modesty!? The Unique Selling Point of the Neelambari lay in the fineness of the yarn and dyeing quality. Very fine hand spun yarn of 250 – 300 s was used for weaving, resulting in a powder fine texture. A heady mix of fine weaving and subtlety of design, the Neelambari was the last word in sophistication. Today traditional handloom sarees woven in Shantipur have 68s to 80s counts cotton yarn in the warp and the weft. Cotton and 2 Aditi Mukherjee, Dec.22,2009, Bengal Handloom.com 3 Aditi Mukherjee, Dec.22,2009, Bengal Handloom.com 4 Bengal Handloom.com silk yarn is used as extra warp in the border, and so is zari. There is also the ?do- rookha? technique of weaving double sided design, where the saree looks same on both the sides. Another unique feature of Shantipur sarees is the finishing. The weavers here use starch (made from sago or popped rice) once while sizing the warp yarn and again, either by hand when the saree is still being woven or by fixing the saree to a frame after weaving is completed. Fulia Tangail: Weavers of Tangail, near Dhaka in modern Bangladesh, were famous for the incomparable Dhakai Jamdani saree. After partition of Bengal during the run up to the independence, the majority of these weavers immigrated to West Bengal, and settled down at Fulia with government patronage. Fulia weavers added a new jest to the handloom weaving scenario in Shantipur region. They developed their own version of the Dhakai, called ?Tangail Jamdani,‘ and a combination of Shantipur and Tangail styles called the ?Fulia Tangail‘. The Tangail Jamdani is similar to the Dhakai Jamdani in that it uses interlocking extra weft cotton yarn to produce floral or geometric motifs. However, it has a softer feel and sparser distribution of motifs. The Fulia Tangail incorporates vibrant colours and large, intricate designs woven in double jacquard. These sarees are also being woven in mulberry and tassar silk apart from cotton. Jamdani: Traditional Jamdani, the pride of Bengal handloom, is now woven in Habibpur and Ramchandrapur near Fulia. The true Jamdani saree is woven without using even a jacquard machine. The weaver uses fine needle-like spindles to conjure magic with extra weft work that can rival the most intricate embroidery. Muslin yardage: Shantipur and its adjoining areas had a tradition of fine muslin yardage weaving, with 600s yarns being used. However, at present there is no major muslin weaving activity in Shantipur. The finest muslins are now woven in Kalna, across the Ganga. It‘s not that the Bengal handloom saree weavers of Shantipur and Fulia have remained confined in a time warp (pardon the pun!). A number of innovations in techniques and products have taken weaving in the region to the next level.
Business of Shantipur:
A. business Partners It has been found that there are some divisions in weaver‘s community. Some of them are master weavers and some are the weavers who work under these master weavers.
Master Weavers - Previously this category of weavers were engaged in weaving only, but today they undertake the overall responsibility of this business from of raw material to the weavers, provide design and pay wages to grass root level weavers; and then supply sarees to Mahajans. Mahajans provide design and information regarding colour combination and a better price realization for the saree, but on the other hand make the transactions on credit. There are around 700 master weavers actively involved in production activities of the cluster. It is estimated that in total, these master weavers have 16,050 working looms, and equal number of weavers working as labours. A part of the production of master weavers is also sold in the local hat i.e. market of Santipur. Most of the weavers do possess 4 looms in one shade. There are few master weavers having 10, 20, 30, 40, 50, 60 looms under one shed. The master weavers apart from the weaving earning of one loom earn profit margins from the products weaved on the loom engaged by the labour. Weavers - There are about 20,000 working looms and 60,000 persons involved directly / indirectly in the weaving and preparatory activities. The women basically undertake the preparatory works like separation of hanks, sizing, pirn winding. Dyers - Dyeing is basically carried out in the dyeing unit. There are about 90 units engaged for dyeing as a commercial activity. These units, based on the quantity of yarn dyed are categorized into large, medium and small units. Designers - There are about 100 small designers involved actively to create and supply new design after exploring their own creativity and imagination in the line of the demand or choice of the consumers. However our definition of modern education does not allow them to be treated as educated. They have their own mechanism to upgrade their own skills. For Lack of exposure their skill are traditional based. Their main role in the cluster is to do costing for the master weaver, and supply them the punch cards for the Jacquard.
b. Steps of business The basic raw material of the cluster is cotton yarn, procured in the form of hank by the weavers / master weavers from the local yarn dealers and Mahajans. Besides cotton yarn the cluster also uses art silk and golden Zari for designing.
Bleaching and Dyeing: The yarns are bleached and dyed in the form of hank and latter dried in sun light putting on bamboo bars.
Sizing: Sizing is a process where starch (Sago or Boiled Rice or Khoi) is coated on the warp yarns for importing strength; enhance abrasion resistance to withstand the stress and strains exerted during weaving process. There by it reduces the yarn breakage and improves quality and efficiency of weaving. The loom sizing is also carried out after weaving to reduce reed marks, to impart stiffness to the fabric to bring into proper look.
Warping and Beaming: The warping is a process of making desired length and width of warp sheet by combining many small packages called bobbins/spools. Sectional warping process is carried on a wooden drum from a wooden peg creel. The Sectional warping process facilitates warp patterning and handling delicates fine spun and filament yarn.
Pirn Winding: After dyeing and sizing of weft yarns, the weft package called pirn is prepared on Charkha. Pirn winding is the process of transferring the yarns from the hanks into bobbin/pirn of the shuttles used in the weft while weaving.
Designing: Designing through jacquard is the most value addition option for the cluster. New Designs are collected from various sources by the Mahajans and converts into new jacquard designs with the help of local designers. Sometimes local designers also introduce some new designers out of their creativity.
Weaving: The weaving is performed by the skilled weavers of the family. The looms being used are mainly traditional fly shuttle pit looms with jacquards. C. Type of business The weaving activity was initiated in 1409, during the regime of Gaur Ganesh Danu Mardhandev. Saree weaving was practiced during 1683 - 1694 during the ruling of Nadia king Rudra Roy.5 The production got systematized and was well organized leading to good recognition during the period of Mughal empire. Saree was exported to Afghanistan, Iran, Arab Greece and Turkey. The healthy trend continued till the early twentieth century. Now the weaving activity has flourished to a large extent. Most of the household are engaged in the weaving activities either as their primary activity or secondary. While observing and studying the area different 5 Feel Handloom.com types of weavers activities are found out. These are discussed below:
Weaver as the Mahajan: These traders initially supply the design and colour combination to the master weavers and the master weaver arranges the production. The traders in turn supply these sarees to the traders of Bara Bazar, Kolkata. From Kolkata these products are distributed to different districts of the state and to other country.
Weaver as the Master Weaver:
Previously this category of weavers were engaged in weaving only, but today they undertake the overall responsibility of supplying the raw material to the weavers, provide the design and pay wages to the grass root level weavers; and then supply the sarees to Mahajans. Mahajans provide design and colour information and a better price realisation for the saree, but on the other hand make the transactions on credit. A part of the production of master weavers is also sold in the haat (local Market) of Santipur. The master weavers apart from the weaving earning of one loom earn profit margins from the products weaved on the loom engaged by the labour.
Weaver as the simple weavers:
These group comes from the middle income group who own at least one loom of their own and do all the works mostly by themselves and sometimes if the situation permits hire labourers. Weavers mainly get orders from the master weavers or the Mahajans and do produce the product in their loom. The women basically undertake the preparatory works like separation of hanks, sizing, pirn winding.
Weaver as the labourers:
There is also this group who comes from a poor economic background work as labour either in the weaver or mostly in the master weaver‘s looms. They generally get their wages on weekly basis depending on the number of products they are producing.
D. profit of business
We have shown here two Statement sheet for two products generally produced in this area one for Scarf and another for Sarees.
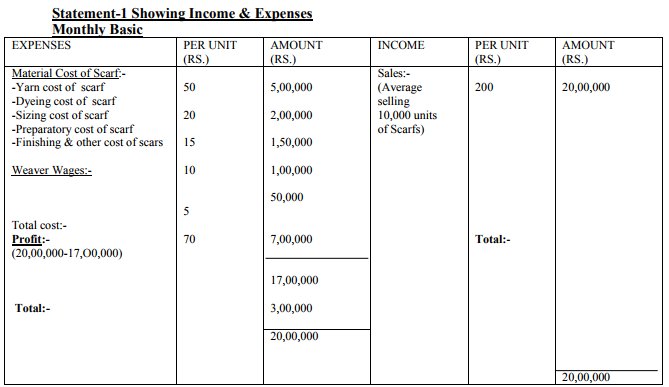
- Total net profit Rs. 3,00,000/-
- Percentage of profit Rs. 15%

Total net profit Rs. 1,180/-
- Percentage of profit Rs. 13.1%
Reflection
Ststement-1 shows that the percentage of material cost and weaver‘s wage are 58.8 and 41.2 respectively. At the time of selling of 10,000 Scarfs the master weaver earn profit Rs.3,00,000 after investing Rs.17,00,000 in a month that is 15 per cent (approx). Daily wage of weavers is Rs.140. In case of Statement -2, for the production of sarees the percentage of material cost and other and weaver wage are 48.8 and 51.2 respectively. The percentage of profit of Master weavers is 13.1 per cent. In case of second activity weavers get around Rs. 133 a day, if he or she wants to offer labour. The demand of weavers in this area is much higher because of the huge rate of margin of profit earn by master weavers. Actually master weavers are paying higher attention to run this business. The wage rate in agricultural sector for unskilled labourer is around Rs. 100 a day. So, ultimately weaving industry is the prime source of livelihood among the poor landless labourer. It is also true that the nature of exploitation by master weavers / middlemen is very high but the weavers have no other alternative. Number of weavers co-operative Societies were formed by the department of Co-operation, Government of West-Bengal with the additional financial help of National Cooperative Development Corporation (NCDC) in this area and naturally they have failed to provide employment opportunity towards land less labourers due to several reasons that is another area of discussion. So the poorer have no other alternatives but to go with the exploiters (master weavers). Our further study may be conducted to find out the way of reducing exploitation of poor, it may be through Public-Private Partnership (PPP) or other.
References:
1. De, Anup. ‘Diagonistic Report of Santipur Handloom Cluster‘, Textiles Committee. [2008], West Bengal.
2. Government of India, ?Census of handlooms in India 1995-96‘, Development Commissioner for Handlooms, Ministry of Textiles, Government of India (1996).
3. Government of India, Report of the Fact Finding Committee (Handlooms and Mills), Ministry of industry and Commerce, 1942
4. Government of India, Report of the High Powered study Team on the problems of the handloom industry, Ministry of Commerce, New Delhi, July, 1974
5. http://feelhandlooms.com [accessed 13 January 2012]
6. http://handlooms.nic.in [accessed 31 December 2011]
7. Jain, Ruby and Rachna Goswami. ?Livelihood Through Handloom Weaving‘, International Research Journal, Vol. I Issue 12. Jaipur. September 2010. ISSN-0975-3486 RNI: RAJBIL 2009/30097.
8. Mitra, Ashis, Choudhuri Kumar, Prabir and Mukherjee Arup. ?A Diagnostic Report on Cluster Development Programme of Shantipur Handloom Cluster: Part 1, Evolution of the cluster and cluster analysis?. Indian Journal of Traditional Knowledge, Vol. 8(4). Visva-Bharati University, sriniketan. Birbhum. October 2009. pp 502-509.
9. Mukherjee, Aditi. ?The Handloom Story of Shantipur-Phulia ?, Blog post, Bengal Handloom website. 22 December 2009 [accessed 7 January 2012].
10. National Sample Survey Organisation 61st Round 2004-05, NSS Report No. 515: Employment and Unemployment Situation in India, New Delhi, September, 2006.
11. Niranjana, Seemanthini and Vinayan, Soumya, ?Report on Growth and Prospects of the Handloom Industry‘. 2001. Planning Commission commissioned study.
Concept of Variables
i) Saree - A dress worn primarily by Hindu women; consists of several yards of light material that is draped around the body. ii) Mahajan - The word "Mahajan" is an amalgam of two Sanskrit words: Maha meaning great, and Jan meaning people or individuals. Over the years, the word Mahajan has come to be used a generic job title that refers to people involved in money lending. iii) Shantipur - It is a city and a municipality in Nadia District in the Indian state of West Bengal. This small town has been declared a city recently. The fort area of this city, also known as DaakGharh (calling or gathering room) is thought to have been built by Raja Krishnachandra of Nadia. is famous for handloom sarees from ancient times. After the partition of India, many weavers came from Dhaka of Bangladesh and started to reside here in Phulia region, which is a Panchayat area of Santipur. iv) Jamdani - It is a type of figured muslin that is one of the greatest accomplishment of the Indian weavers. The origin of figured muslin is not clear. It is mentioned in the Sanskrit literature of Gupta period (4th – 6 th century AD). It is known that in the Mughal period the finest Jamdani were produced in Dhaka (Bangladesh), the work being characterised by extremely elaborate designs. Nowadays there are two types of Jamdanis are available i.e., Dhakai Jamdani and Tangail Jamdani. v) Zari - Zari (or Jari as traditionally called) is basically a tinsel thread meant for weaving and embroidery. vi) Scarf - A scarf is a piece of fabric worn around the neck, or near the head or around the waist for warmth, cleanliness, fashion or for religious reasons. They can come in a variety of different colours.
|