IJCRR - 5(7), April, 2013
Pages: 124-131
Date of Publication: 18-Apr-2013
Print Article
Download XML Download PDF
COMPRESSIVE STRENGTH AND HEATING VALUES EVALUATION OF THE INDIGENEOUS COAL BRIQUETTES OF PAKISTAN (KPK PROVINCE)
Author: Unsia Habib, Amad Ullah Khan, Muddasar Habib
Category: Technology
Abstract:Pakistan has significant amounts of coal reserves but the country is largely dependent upon the petroleum products and natural gas for their energy needs because of the lack of the large scale technologies to exploit the local coal reserves. The coal Briquetting is one of the small scale technology to use the local coal for various applications. In the current study the coal briquettes were developed by using the coal of the Khyber Pakhtun Khwa province of Pakistan and their strength and thermal properties were evaluated. A small scale experimental unit was made locally for the formation of coal briquettes. Polyvinyl acetate (PVA) binder was chosen for making briquettes because of its good binding characteristics and its organic nature that helped in increasing the mechanical strength and the combustion characteristics of coal briquettes. Different briquettes of the same size and shape were formed by using changing the composition of PVA binder. The mechanical strength of coal briquettes was measured by compressing the Briquetting by applying external load on them until their breaking points. The load required and deflection produced by the briquettes at their yield and break points was found out and a comparison was made among briquettes to identify the high strength briquettes. The thermal properties were measured for all the briquettes by finding out their calorific value. The results show that the thermal properties and strength was the maximum for the briquette no 4 with a composition of 165 ml of PVA binder mixed with 220 ml of water as solvent in 1kg of coal in this work.
Keywords: Coal briquettes, Binder, strength of coal briquettes, calorific value of coal briquettes, alternative energy source
Full Text:
INTRODUCTION
The development of a nation needs a persistent supply of energy resources. The problem of energy crisis is increasing day by day in the developing countries like Pakistan. The reservoirs of conventional energy resources as petroleum and natural gas have greatly reduced and the country is largely dependent on the import of fuel to meet their energy needs [1]. The use of alternative fuel sources has been proposed from time to time to overcome this issue. Coal is an important energy source and is present in considerable amounts in Pakistan particularly in the province of KhyberPakhtun Khwa (KPK) [2] . Coal reserves of can be used effectively in the form of coal briquettes on a small scale to meet the energy needs of everyday life. Coal Briquetting is a technique to convert raw coal powder into a definite shape. A binder is used to hold or bind the coal particles together in the desired shape. Coal briquettes are better fuel than the raw coal because of their enhanced mechanical and thermal properties. The addition of some binders and other additives not only increases the strength and the heating value of the coal briquettes but also greatly suppresses the emission of poisonous gases in the environment [3]. Coal briquettes have reduced contribution towards the environmental pollution as compared to raw coal and other traditional fuels present in Pakistan like wood, animal dung and charcoal [4]. The coal briquettes can be made indigenously and can serve as a fuel source to meet various domestic and commercial purposes in the developing countries as Pakistan [5]. The performance of coal briquettes is evaluated by its strength and thermal properties. The Mechanical strength is an important parameter in the evaluation of coal briquettes because it affects their storage and the transportation process. The high strength briquettes can be easily transported to the market and their storage and handling process is also easy at the site of usage.The strength of the coal briquettes is dependent upon many factors like type of coal,size of coal used for making briquettes, the type of binder, curing temperature etc. The studies show that reducing the size of raw coal used for briquettes making enhances their strength [6,7,8]. The heat treatment before making briquettes has also found to increase the mechanical and thermal properties of coal briquettes [9]. The type and amount of binder greatly influence the strength and combustion characteristics of the coal briquettes. The use of petroleum products and the coal tar pitch as binder gives high strength briquettes but they are not favorable because they emit poisonous gases on burning and have some adverse effects on the human beings [10]. On the other hand the natural cellulose binders as molasses, saw dust etc. generates less emission but their strength is comparatively lower [10]. In this work Poly vinyl acetate (PVA) was used as a binder in producing briquettes. PVA binder was selected because it is organic in nature so it will not degrade the environment and also because it is locally available at low-price. The compressive strength and the combustion properties of the raw coal and the coal briquettes made were assessed in this work. The strength of the briquettes was measured by applying load on them and their deflection values under the applied load. The values of the load required to break the briquettes and the maximum load that a body can withstand defines its strength, so these values were measured. The thermal properties of the briquettes were determined by measuring the calorific values of the briquettes formed and a comparison was made among the briquettes to recognize the briquette with high strength and high heating value.
MATERIAL AND METHODS
Raw Materials
The indigenous coal samples from KPK (Khyber Pakhtun Khwa ) Province of Pakistan were used in this work. Polyvinyl Acetate was selected as a binder for making coal briquettes . The binder was selected because PVA has good adhesive properties and because it was easily available in the market at low rates.
Experimental Setup
The Briquetting machine required for producing briquettes was formed locally in the Department of Chemical Engineering UET Peshawar. The design of the Briquetting machine is simple and consists of three main parts i.e Frame, mold and a handle.The frame is used to hold up the other parts of the machine. The mold is the main part of the Briquetting machine in which the coal briquettes are given required shape by putting coal and the binder mixture in it .The cylindrical shape mold with small holes is used in this work.The length of the mold was 200 mm and the inside diameter of the cylindrical mold was 120mm. The small holes present in the mold were 12 in number with a diameter of 10 mm. A long handle is attached to the head of the mold to press the coal mixture inside the mold by applying manual force on the handle. Finally when the coal mixtures acquired the definite cylindrical shape inside the mold, the briquettes were removed from the machine and were kept in the sun for drying. The Briquetting machine used for this work is shown in the Figure 1
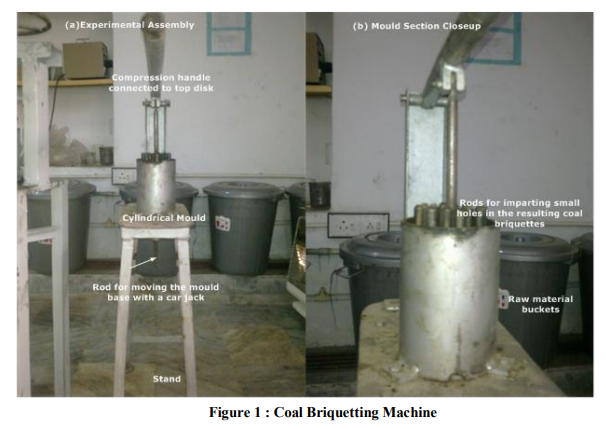
The Briquettes made were then tested for their strength in the universal testing machine (UTM). The briquette to be tested was placed in the UTM and the external load was applied on it to compress it. The value of the load was gradually increased and the deflection produced in the briquettes was measured through a computer interface connected with the UTM. . The load and deflection values at the yield and break points of briquettes were identified this way. The maximum load that a material can bear and its corresponding deflection value was also found out. The values obtained were then compared with each other to recognize the composition of high strength briquettes. The comparison of the combustion characteristics was measured by finding the calorific value of the briquettes in the oxygen bomb calorimeter.
Briquette Formation
The first step in the formation of coal briquettes was the preparation of binder. Five samples of binders were made with different amounts of PVA mixed with the water to make a binder solution. The coal powder was then screened through 200 mm steel mesh to a get a coal sample of uniform size. The amounts of binder, water and coal powder for different briquettes are presented in the table 1.
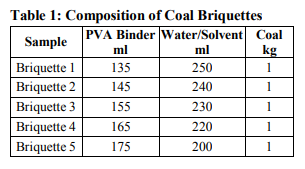
The coal powder was then mixed with the binder solutions manually. The mixture of coal and binder was then poured into the Briquetting press to get the coal briquettes of desired shape. The briquettes formed were then dried in the sun for 2 days. The coal briquettes formation steps are summarized in the figure 2.
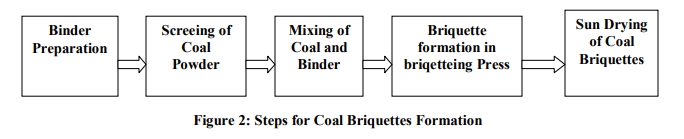
RESULTS AND DISCUSSIONS
The dimensions of cylindrical coal briquettes produced in the study are presented in the table 2.
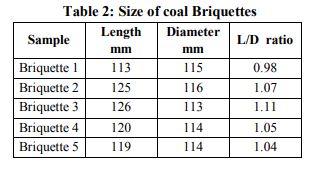
The data in the table III show that there is a slight difference in the L/ D ratios of all the briquettes so all the briquettes have nearly the same size . The relationship of load and deflection produced in all the briquettes as a result of compression force acted upon them are represented in the graphs below.
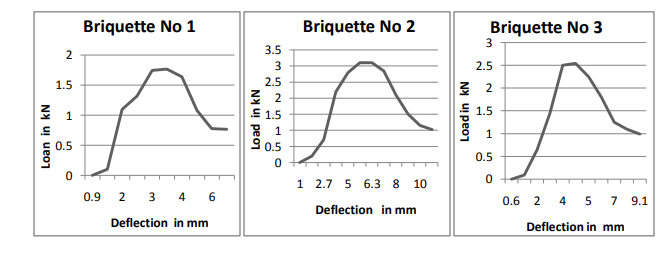
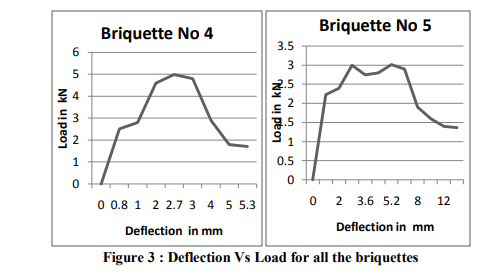
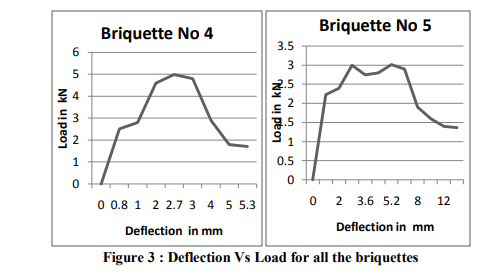
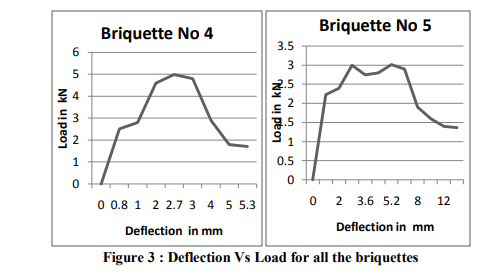
The load and deflection graphs of all the briquettes follow a somewhat parabolic trend. The highest variation from the parabolic trend is displayed in the briquette No 5 because of its zig zag pattern .The Briquettes No 1, 2,and 3 shows deflection without any load in the beginning while briquette no 4 and 5 shows deflection when the load is applied to them. It is also evident from the graphs that less load is required for all the briquettes after the maximum point to produce a further deflection in the briquettes and this value keeps on deceasing until the break point is reached. All the briquettes in this work show a significant decrease in their load values after their maximum point. The purpose of finding the load and deflection relationship is to identify the yield, break point and the maximum point. These values are then plotted for all the briquettes to recognize their strengths and have a comparison of these values.
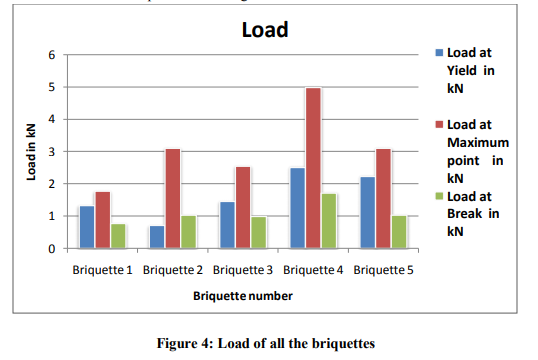
The load graph shows that the briquette No 4 have the highest yield, maximum and the break values which means that more force (in the form of external load ) is required to break the briquette no 4 as compared to other briquettes. Hence briquette No 4 have the maximum strength among all the briquettes. Based on the values of load at yield, break and maximum point the briquettes can be arranged in the following way Briquette no 4 > Briquette no 5> Briquette no 2 > Briquette no 3 > Briquette no 1. Further the deflection values are also compared with each other and are presented in figure 5.
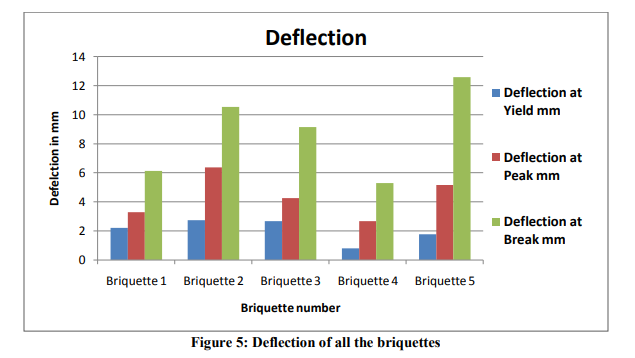
The deflection graph shows that the maximum deflection at their yield, maximum and break points is shown by briquette no 5 which means that briquette no 5 is displaced to higher degree under the action of applied load. The lowest amount of deflection is shown by briquette no 4 which means that the briquette no 4 does not dislocate much when load is acted upon it. The high value of deflection shown by briquette no 5 means that it is the most flexible briquette and briquette no 4 is the most rigid or the tough briquette among all the briquettes. All the other briquette shows deflection values in the temperate range. The combustion characteristics of all the briquettes are shown by measuring their gross calorific values. The values obtained are presented in the figure 6.
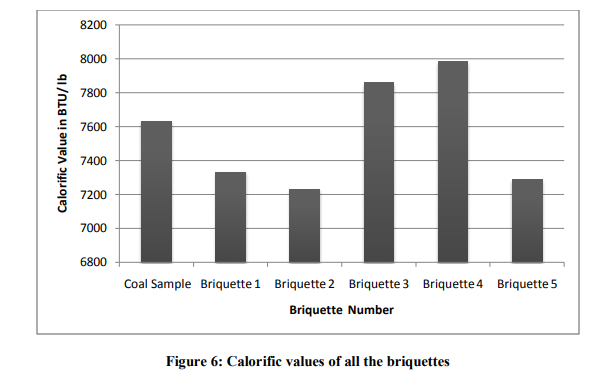
The calorific value data show that the heating value of the briquette no 3 and 4 is greater than the raw coal which means that the PVC binder when added in the ratio as given by the composition of briquette no 3 and 4 results in enhancing the thermal properties of the coal briquettes. The higher heating value is obtained by the briquette no 4 while the lowest value is of briquette no 2.
CONCLUSIONS
Based on the results provided in this study it can be concluded that, in the absence of any centrally administered coal power generating plant, KPK coal can be effectively used in the form of coal Briquettes. A simple Briquetting press can be developed indigenously for local on site use. Cylindrical shaped briquettes of nearly identical size were made by using PVA as a binder in this work. PVA binder was found to increase the mechanical strength of all prepared briquettes. The combustion characteristics of some briquettes were also enhanced by the addition of PVA binder. The results showed that the thermal properties and strength were maximum for briquette no 4 sample which had a composition of 165 ml of PVA binder mixed with 220 ml of water as solvent and mixed with 1kilogram of raw coal powder for making a cylindrical shaped compressed briquette.
ACKNOWLEDGMENT
The authors acknowledge the immense help received from the scholars whose articles are cited and included in references of this manuscript. The authors are also grateful to authors / editors / publishers of all those articles, journals and books from where the literature for this article has been reviewed and discussed.
References:
1. Malik. A. Crude oil price, monetary policy and output, case of Pakistan. The Pakistan Development Review 2008 ;47 (4) : 425–36.
2. Laurance J. D, Geological investigations at a high altitude, remote coal mine on the Northwest Pakistan and Afghanistan frontier, Karakoram Himalaya, Int J of Coal Geology 2004 ; 60 : 117–50.
3. Zhao Y, Chen L .Environmental protecting effect of industrial coal briquette, Proceedings of the Sixteenth Annual International Pittsburgh Coal Conference ,1999 Oct 11-15 ; Pittsburgh, PA (US) : 1999.
4. Wachter, E. A , Gammage R. B., Haas J. W, Wilson D.L , DePriest J.C, Wade.J, N. Ahmad N , Sibtain F,Raza M.Z. Impact on indoor air quality during burning of Pakistani coal briquettes, Environment International 1993 ; 19 ( 2) : 133–45.
5. Guorui. Z, Conghu .P, Yingjun .C, Dongyan Liu, Guoying. S , Jiamo.F , Deployment of coal briquettes and improved stoves: possibly an option for both environment and climate, Environmental Sci and Tech. , American Chemical Society 2009 ; 43 (15) : 5586 - 91.
6. Berkowitz N. Fundamental aspects of coal Briquetting. Proceedings of the 3rd Biennial Conference, IBA.1953.
7. H.R. Gregory. A new process for briquetting coal without a binder. J Institute of Fuel 1960 ; 33 : 447-61.
8. Motaung S.R, Mangena S.J , de Korte J.G, McCrindle R.I , van Heerden J.H.P . Effects of Coal Composition and Flotation Reagents on the Water Resistance of Binderless Briquettes. Coal Preparation. 2007 ; 27(4) : 230-48.
9. BlesaM.J, Miranda J.L , Moliner.R ,Izquierdo M.T. Curing temperature effect on the mechanical strength of smokeless fuel briquettes prepared with molasses. Fuel 2003 ; 82 : 943-47.
10. Altun N.E, Hicyilmaz. C, Bagci A. S. Influence of coal briquette size on combustion kinetics. Fuel Processing Tech 2004 ; 85 : 1345-57.
|